Comprehensive Guide to GRP in Modern Business Applications
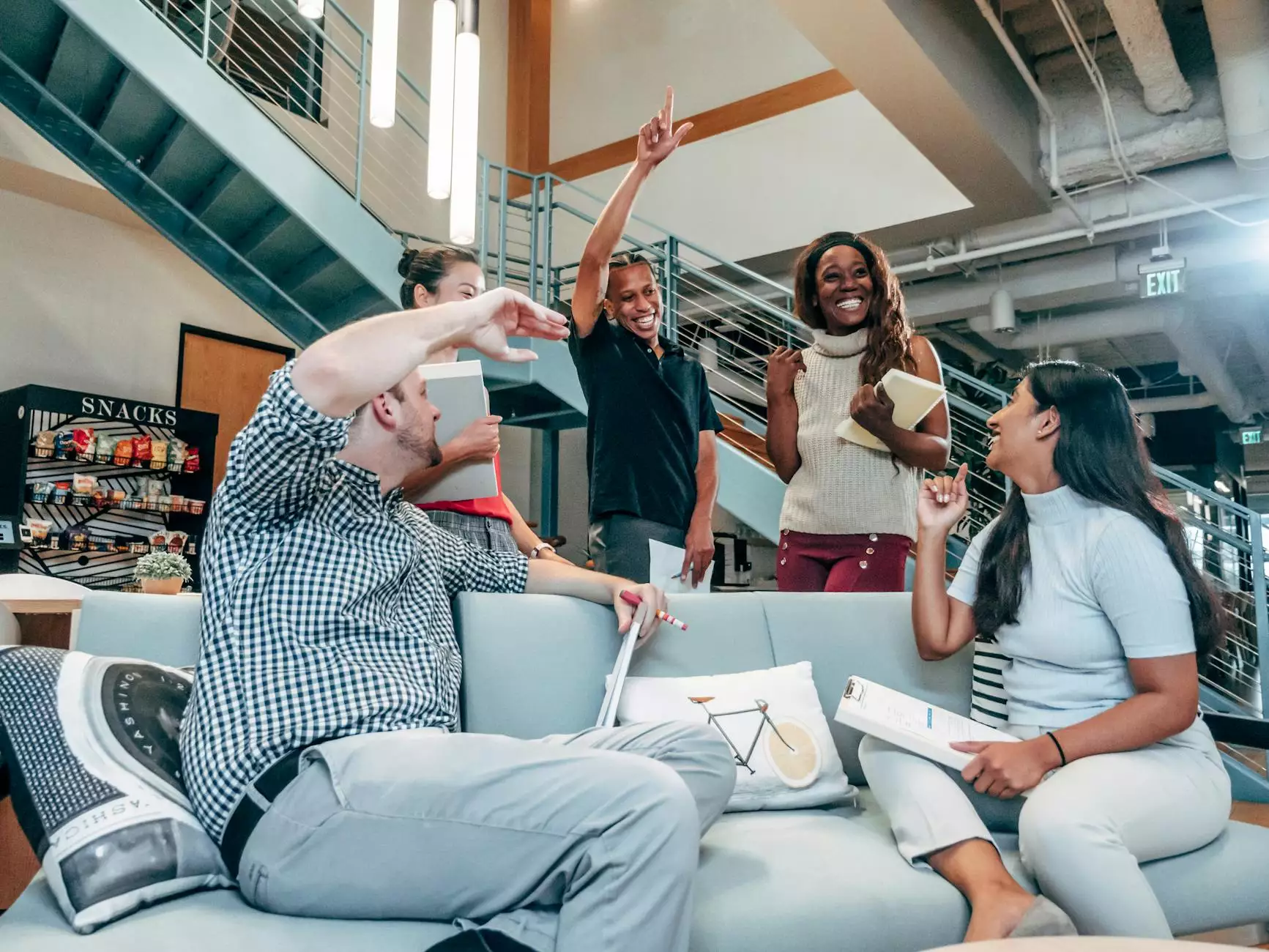
In the rapidly evolving world of manufacturing and business solutions, Glass Reinforced Plastic (GRP) has emerged as a cornerstone material, delivering unmatched versatility, strength, and durability. As industries ranging from construction to automotive increasingly seek innovative, sustainable, and cost-effective materials, GRP stands out as a premier choice. This guide aims to provide an in-depth understanding of GRP, its applications, advantages, and how businesses like Celtic Composites UK harness this technology to drive growth and efficiency.
What Is GRP? An In-Depth Explanation
GRP, or Glass Reinforced Plastic, also known as Fiberglass in many regions, is a composite material formed by combining glass fibers with a resin matrix, typically polyester, vinyl ester, or epoxy. This synergy results in a material renowned for its exceptional properties, including high strength-to-weight ratio, corrosion resistance, and design flexibility.
The manufacturing process of GRP involves laying the glass fibers into molds or forms, then impregnating them with resin. Once cured, these materials form solid, durable structures suitable for a myriad of applications. The versatility of GRP allows it to be molded into complex shapes, making it ideal across various industries.
The Extensive Applications of GRP in Business Sectors
- Construction and Infrastructure: Utilized for cladding, roofing, pipes, and architectural elements due to its weather resistance and ease of fabrication.
- Transportation: Used in the manufacturing of boat hulls, vehicle parts, and aircraft components because of its lightweight yet robust characteristics.
- Industrial Equipment: Serves as tanks, ducts, and piping in chemical plants and water treatment facilities owing to its corrosion resistance.
- Renewable Energy: Employed in constructing wind turbine blades thanks to its high strength and flexibility.
- Decorative and Consumer Goods: In furniture, sports equipment, and leisure products, offering innovative design possibilities.
Advantages of Using GRP in Business Operations
Enhanced Durability: One of the key advantages of GRP is its resistance to corrosion, weathering, and chemical attacks, which ensures longevity even in harsh environments.
Lightweight Construction: Compared to traditional materials like steel or concrete, GRP offers remarkable weight savings, facilitating easier installation, transportation, and handling.
Design Flexibility: Thanks to its mouldability, GRP allows for the production of complex shapes and detailed features that are challenging with conventional materials.
Cost-Effectiveness: Although initial manufacturing costs can be higher, the durability and low maintenance requirements lead to significant savings over the lifecycle of the product.
Environmental Benefits: The production and recycling of GRP contribute to sustainable practices, as the material can be designed for recyclability and reduced waste.
Innovative Manufacturing Techniques in GRP Production
Modern GRP manufacturing employs several advanced techniques to optimize quality and efficiency:
- Open Moulding: A traditional method where resin is applied into open molds, ideal for large or simple parts.
- Closed Moulding: Encompasses processes like vacuum infusion and resin transfer molding, providing high-quality, consistent parts with minimal voids.
- Pultrusion: Continuous process creating long, uniform profiles for structural applications.
- Spray-Up and Hand Layup: Cost-effective methods suitable for custom or low-volume parts with intricate shapes.
Each manufacturing method allows businesses to tailor GRP components precisely to project needs, optimizing performance and cost.
Design and Engineering Considerations for GRP Applications
Material Selection and Resin Types
The choice of resin impacts the GRP properties significantly. Polyester resins are economical and widely used, while epoxy resins offer superior mechanical strength and chemical resistance. Vinyl ester resins provide a middle ground with excellent corrosion resistance and affordability.
Structural Design
Proper design considers fiber orientation, lamination schedules, and resin content to maximize strength, flexibility, and weight savings. Engineers must balance stiffness with weight, accounting for environmental stresses such as wind, load-bearing requirements, and chemical exposure.
Quality Control and Testing
High standards of quality assurance, including non-destructive testing, tensile strength, and UV resistance evaluations, ensure GRP components perform reliably over their lifespan.
Case Study: Celtic Composites UK and Their Use of GRP
Celtic Composites UK exemplifies industry leadership by leveraging GRP in manufacturing solutions that meet rigorous standards. Their commitment to innovation allows for customized products that serve clients across various sectors, including marine, construction, and industrial markets.
By employing cutting-edge manufacturing techniques such as resin infusion and pultrusion, Celtic Composites UK ensures the highest quality GRP components that withstand the test of time and environmental challenges. Their dedicated R&D team constantly innovates, integrating sustainable practices and advanced materials into their processes.
Future Trends in the GRP Industry and Business Opportunities
- Advanced Composite Technologies: Incorporation of nanomaterials and bio-based resins to improve strength, sustainability, and environmental friendliness.
- Digital Fabrication: Use of AI-driven design and automated manufacturing to optimize efficiency and customization capabilities.
- Eco-Friendly Practices: Developing recyclable GRP formulations and reducing carbon footprints in production.
- Expanding Markets: Growing demand in renewable energy, water management, and lightweight automotive parts opens new avenues for GRP adoption.
Why Businesses Should Invest in GRP Today
Investing in GRP technology offers a competitive edge through superior durability, flexibility, and cost savings. Companies aiming to innovate and adapt to environmental demands will find GRP a vital asset in their material portfolio.
Partnering with experienced manufacturers like Celtic Composites UK ensures access to high-quality GRP solutions, tailored to specific industry needs. This strategic move enables businesses to enhance product longevity, reduce maintenance costs, and meet sustainability goals simultaneously.
Conclusion: Embracing the Power of GRP for Sustainable Business Growth
From its inception as a high-performance composite material, GRP has evolved into a critical component across diverse industries. The combination of its lightweight nature, exceptional resistance properties, and manufacturing versatility makes it an invaluable asset for forward-thinking companies.
By understanding the technical nuances, applications, and future opportunities within the GRP industry, businesses position themselves at the forefront of innovation. Celtic Composites UK exemplifies how leveraging GRP can lead to sustainable growth, operational excellence, and competitive advantages.
If your organization is ready to harness the potential of GRP, consider collaborating with industry leaders who prioritize quality, sustainability, and innovation. The future of business is resilient, adaptable, and built upon the strength of materials like GRP.