The Rising Importance of Plastic Injection Mould Manufacturers
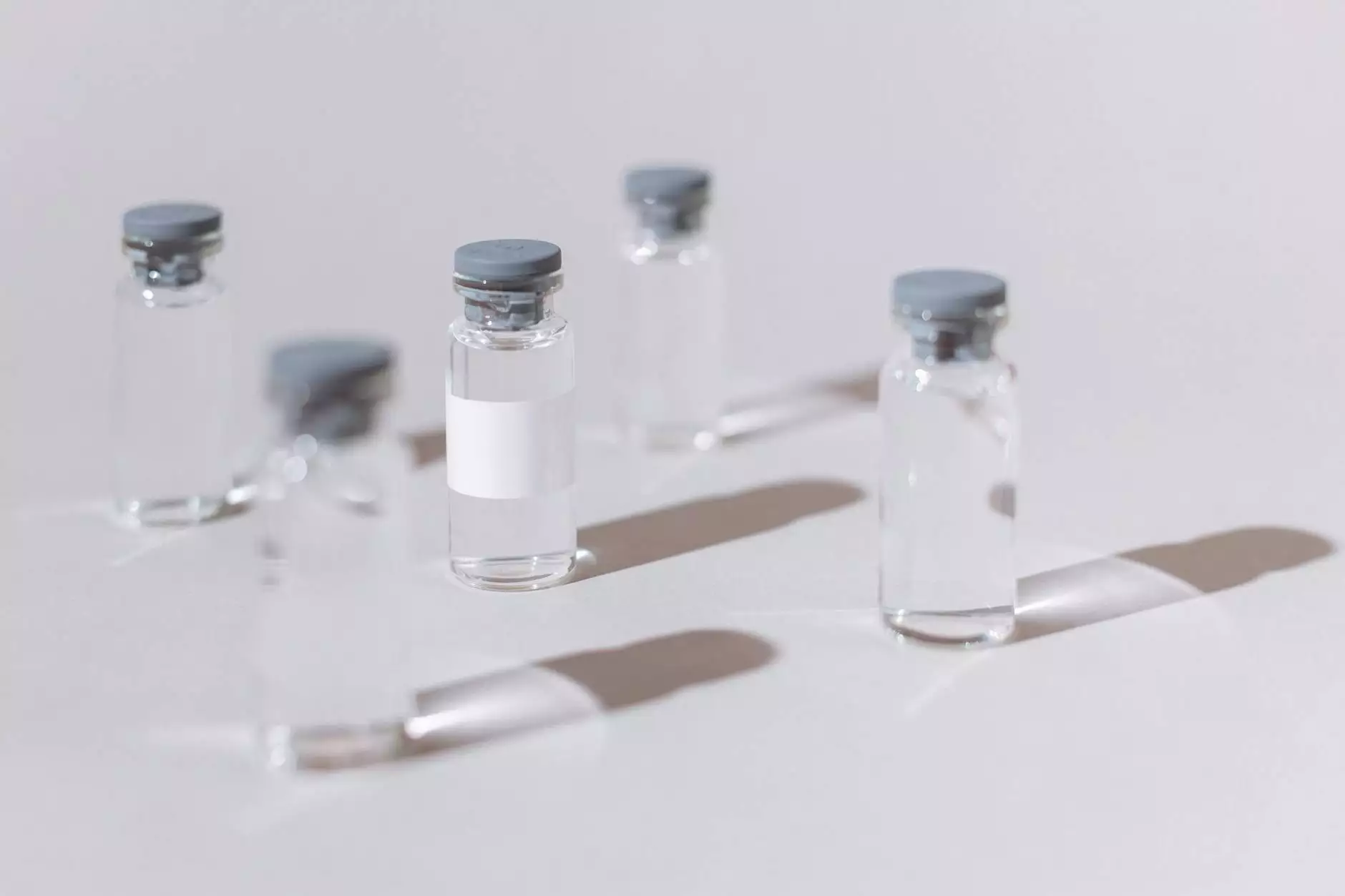
In today’s fast-paced manufacturing landscape, the demand for efficient, cost-effective, and high-quality production processes is at an all-time high. One of the cornerstones of modern manufacturing is the process of plastic injection moulding. This technique is fundamental for producing a vast array of plastic components used in diverse industries, from automotive to consumer goods. As a result, the role of plastic injection mould manufacturers has become increasingly significant, providing essential services that support innovation and production efficiency.
Understanding the Process of Plastic Injection Moulding
Plastic injection moulding is a manufacturing process that involves the injection of molten plastic into a mould to create a specific shape. This method is praised for its ability to produce large quantities of identical items quickly and efficiently. The process can be broken down into several key stages:
- Designing the Mould: The first step involves designing a mould that can withstand the high pressure and temperature of the injection process. This includes selecting the appropriate materials and ensuring the design allows for optimal flow of the molten plastic.
- Melting the Plastic: Raw plastic pellets are heated until they melt, transitioning into a viscous liquid suitable for injection.
- Injecting the Plastic: The molten plastic is injected into the mould at high pressure, filling all necessary cavities.
- Cooling and Solidifying: Once the mould is filled, it is cooled to allow the plastic to solidify, taking on the shape of the mould.
- Demoulding: After cooling, the mould is opened, and the final product is ejected.
The Benefits of Plastic Injection Moulding
The advantages of using plastic injection moulding are numerous and can greatly benefit manufacturers and consumers alike. Here are some of the key benefits:
- Efficiency: Once the moulds are created, production can occur rapidly, making it suitable for high-volume manufacturing.
- Cost-Effectiveness: The initial cost of designing moulds can be high, but the cost per unit decreases significantly with mass production.
- Precision and Quality: Injection moulding offers high precision and consistency, minimizing waste and ensuring each product meets specified tolerances.
- Material Versatility: A wide range of plastics can be used, allowing for customization based on the needs of the industry.
- Complex Geometries: The process allows for the creation of complex shapes that would be difficult or impossible with other manufacturing methods.