Electric Injection Molding: Revolutionizing the Metal Fabrication Industry
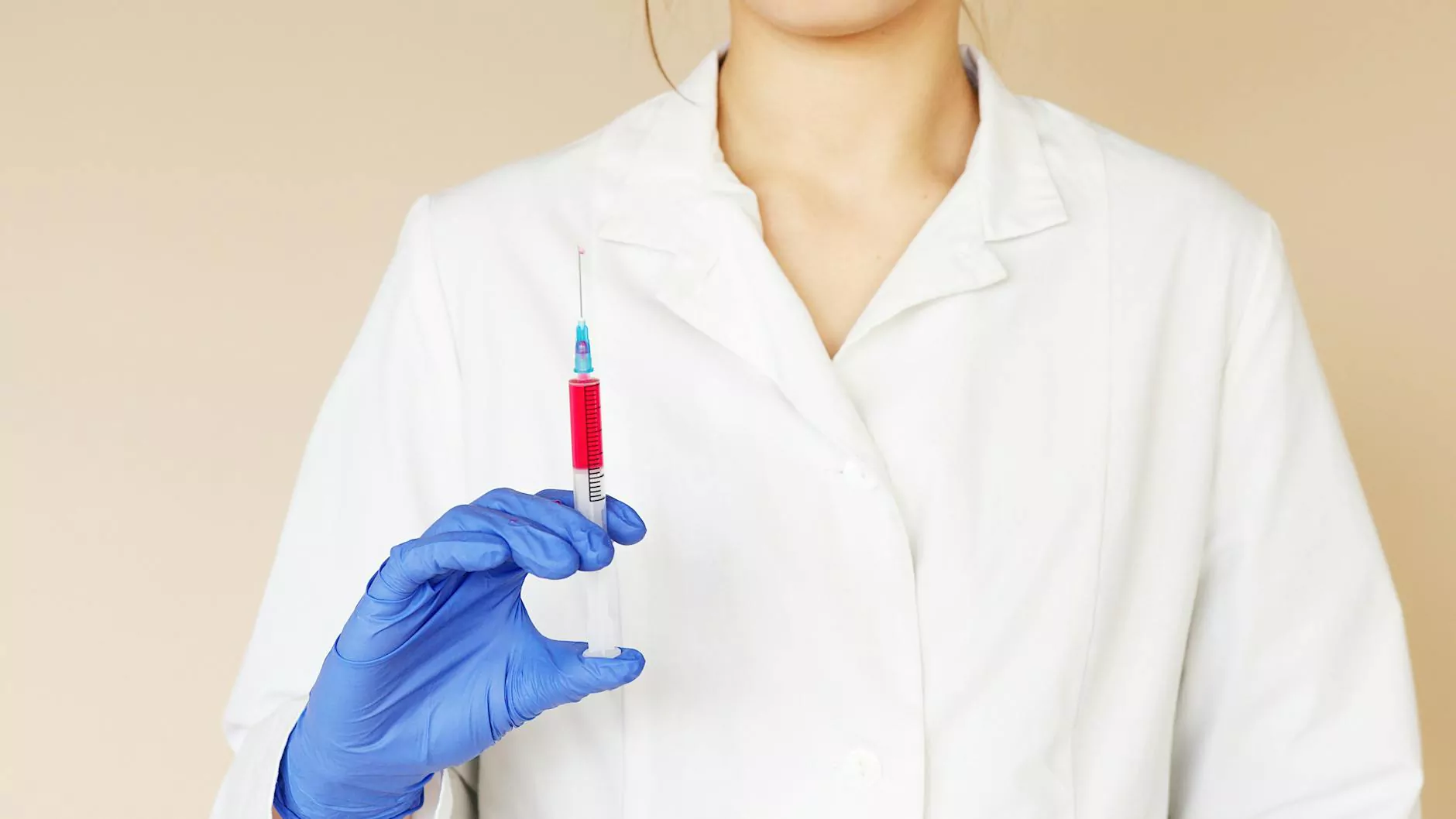
Electric injection molding has been a game-changer in the manufacturing sector. As a key process used in the production of various plastic and metal components, its rise in popularity is particularly evident in the world of manufacturing and metal fabrication. This article delves deep into the intricacies of electric injection molding, examining its benefits, applications, and how it stands to redefine the landscape of metal fabricators.
Understanding Electric Injection Molding
Electric injection molding is a process where molten material is injected into a mold cavity with high precision and control. Unlike hydraulic injection molding, which relies on hydraulic pressure to drive the injection process, electric injection molding utilizes electric actuators and servo motors for enhanced efficiency and accuracy. This technology is particularly significant for metal fabricators looking to produce intricate parts with minimal tolerance variations.
The Working Mechanism of Electric Injection Molding
The process of electric injection molding involves several key steps:
- Material Preparation: Raw material, typically in the form of pellets, is fed into a hopper. Here, it is heated until it melts into a viscous liquid.
- Injection Phase: The molten material is injected into the mold cavity under high pressure. The use of electric actuators allows for precise control of both speed and pressure, ensuring excellent fill characteristics.
- Cooling: Once the mold is filled, the material is allowed to cool and solidify. The cooling process is critical, as it influences the final properties of the molded part.
- Mold Opening and Ejection: After sufficient cooling, the mold opens, and the freshly molded part is ejected. The precise control available in electric molds minimizes defects during this phase.
Advantages of Electric Injection Molding
Electric injection molding offers several compelling advantages that sets it apart from traditional methods, making it an attractive option for metal fabricators:
- Energy Efficiency: Electric injection molding uses significantly less energy than hydraulic systems. This not only reduces operational costs but also lowers the environmental impact of manufacturing processes.
- Precision and Control: The absence of hydraulic fluids means that electric machines can provide tighter control over key parameters, resulting in parts with consistent quality and reduced scrap rates.
- Reduced Maintenance: Electric systems generally require less maintenance than hydraulic systems. With fewer moving parts and no need for hydraulic fluid, the overall wear and tear on machinery are minimized.
- Faster Cycle Times: Electric injection machines can achieve faster cycle times due to their rapid response capabilities, leading to increased productivity for manufacturers.
Applications of Electric Injection Molding in Metal Fabrication
The versatility of electric injection molding serves various sectors, particularly in metal fabrication:
Aerospace Manufacturing
In the aerospace industry, components must adhere to stringent dimensional tolerances and safety standards. Electric injection molding can produce lightweight, strong components that meet these high requirements with consistent quality.
Automotive Components
The automotive industry benefits immensely from electric injection molding by producing complex parts with high strength-to-weight ratios. The ability to utilize specialty materials such as reinforced thermoplastics further enhances the performance of automotive parts.
Electronics Packaging
As manufacturers strive for smaller, more efficient designs, electric injection molding plays a crucial role in producing compact and intricately designed electronics enclosures, ensuring functionality without compromising on protection.
Future Trends in Electric Injection Molding
As technology continues to evolve, so too does the field of electric injection molding. Some anticipated trends that will shape the future of this process include:
Smart Manufacturing and Industry 4.0
With the advent of Industry 4.0, electric injection molding is poised to take advantage of smart technologies, including IoT and AI. These innovations will facilitate real-time data collection and analysis during the injection molding process, thus enhancing operational efficiency.
Advanced Materials
Ongoing developments in material science will enable the introduction of new composite materials tailored for electric injection molding. Research continues to focus on alloys and plastics that can withstand higher temperatures and strains, broadening the scope of applications across different industries.
Sustainability Initiatives
As environmental concerns become more pronounced, manufacturers are increasingly prioritizing sustainability. Electric injection molding can lead the charge in creating eco-friendly products by optimizing energy usage and reducing waste.
Conclusion: The Promising Future of Electric Injection Molding for Metal Fabricators
Electric injection molding represents a significant leap forward for metal fabricators. Its advantages in energy efficiency, precision, and reduced maintenance costs make it an ideal solution in various applications ranging from automotive to aerospace. As we move closer to an era dominated by smart manufacturing and innovative materials, electric injection molding stands out as a pivotal technology that will shape the future of manufacturing.
With continuous advancements, the incorporation of this technology can enable manufacturers to not only enhance production efficiency but also maintain their competitive edge in an ever-evolving market. For those in the metal fabrication industry, embracing electric injection molding could very well be the key to unlocking greater productivity and product quality.
Learn More About Electric Injection Molding
If you're interested in exploring more about electric injection molding and how it can benefit your business, visit DeepMould.net and discover tailored solutions that address your specific manufacturing needs.