Understanding LEV Testing and Its Importance for Businesses
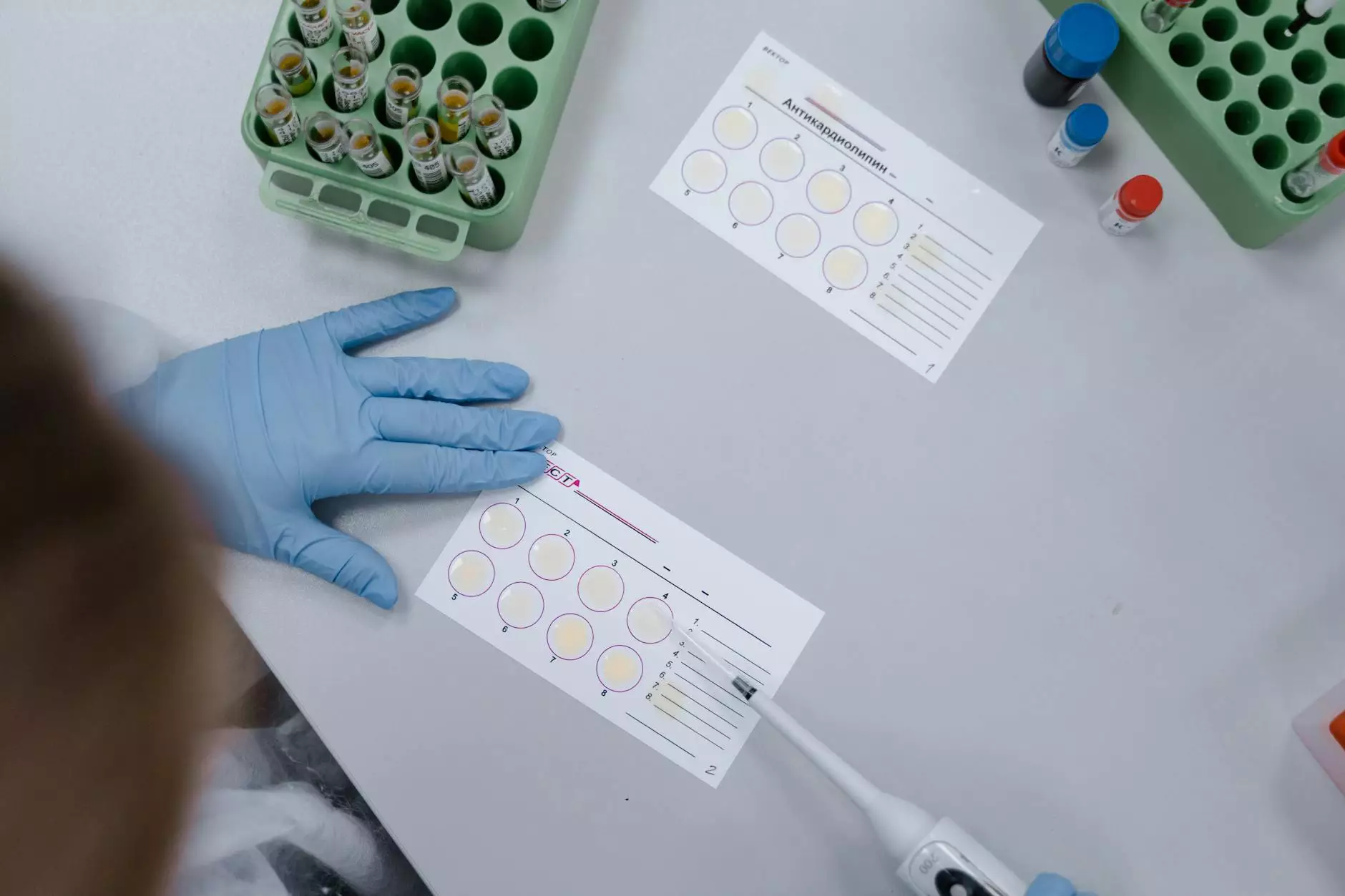
In today's rapidly evolving business environment, especially in sectors like Home & Garden, Gardening, and Pest Control, ensuring the safety and wellbeing of both employees and customers is paramount. One critical element in achieving this is through LEV testing, which stands for Local Exhaust Ventilation testing. As a business owner or manager, knowing the ins and outs of LEV testing can not only safeguard your workforce but can also significantly enhance your business's reputation and compliance with health standards.
The Basics of LEV Testing
What is LEV Testing?
LEV testing is a process that assesses the effectiveness of local exhaust ventilation systems which are designed to remove airborne contaminants from the workplace. These systems are critical in industries where hazardous substances are present, including fumes, dust, aerosols, and vapors. Regular testing ensures that these systems are functioning properly and provides a safe working environment.
Why is LEV Testing Necessary?
- Compliance with Regulations: Businesses are legally required to comply with health and safety regulations, which include adequate ventilation measures.
- Health and Safety of Employees: Ensuring that workers are not exposed to harmful substances prevents occupational diseases and enhances employee wellbeing.
- Operational Efficiency: A well-maintained LEV system can improve productivity by ensuring clean air and a safe working environment.
- Reputation Management: Companies that prioritize employee safety enhance their reputation, leading to increased customer trust and loyalty.
Specific Considerations for the Home & Garden Sector
The Role of LEV Testing in Home & Garden Businesses
In the Home & Garden industry, businesses often deal with a variety of materials that can release harmful substances, especially during activities like gardening and pest control. For example:
- Pesticides and Herbicides: When applying these chemicals, proper ventilation is essential to ensure that airborne toxins are kept to a minimum.
- Soil and Plant Dust: Dust from soil and certain plant materials can be a respiratory hazard, making effective LEV systems vital.
Understanding the Risks
Failure to conduct regular LEV testing can lead to serious health implications for employees. This can result in long-term health issues such as chronic respiratory diseases or chemical exposure problems. Moreover, by neglecting testing, businesses risk facing penalties or litigation due to non-compliance with safety standards.
A Comprehensive Step-by-Step Guide to LEV Testing
1. Identify Your LEV Systems
The first step is to identify all local exhaust ventilation systems in your workplace. This includes fume cupboards, downdraught tables, and extractor hoods. Ensure that you have a clear record of where they are located and their intended uses.
2. Schedule Regular Testing
Establish a clear schedule for conducting LEV testing. This is typically recommended annually, but more frequent testing may be necessary depending on the intensity of use or materials handled.
3. Engage a Professional Service
While some companies may attempt to conduct LEV testing in-house, it’s often best to engage a qualified professional who specializes in this testing. They bring expertise and can provide accurate assessments and recommendations.
4. Complete a Thorough Assessment
During the testing, various parameters will be evaluated, including:
- Airflow rates
- Filter effectiveness
- Noise levels of the system
- Location and efficiency of the extraction points
5. Implement Recommendations
After testing, you will receive a report detailing the system's performance and any recommendations for improvements. It’s important to act on these promptly to maintain compliance and safety.
6. Maintain Documentation
Keep comprehensive records of all testing dates, results, and any actions taken. This documentation is crucial for compliance audits and can serve as proof of diligence in protecting your employees' health.
Lev Testing in Pest Control Businesses
Importance for Pest Control Professionals
Pest control companies face unique challenges in terms of airborne contaminants. The use of chemical pesticides necessitates rigorous LEV testing to avoid potential health hazards. Here are some specific factors to consider:
- Chemical Exposure: Inadequate LEV systems can lead to significant exposure to toxic chemicals.
- Respiratory Risks: Employees may develop respiratory problems if proper ventilation is not maintained while applying pest control substances.
- Customer Safety: Ensuring effective ventilation during pest control services not only protects employees but also reassures clients regarding their safety.
Best Practices for Pest Control Businesses
To ensure the highest standards of safety and compliance, pest control businesses should:
- Adhere strictly to local regulations regarding pesticide application and LEV systems.
- Provide training for staff on the importance of effective LEV systems and personal protective equipment.
- Regularly review and update their safety protocols to incorporate the latest industry best practices.
Conclusion: Make LEV Testing a Priority
In conclusion, conducting regular LEV testing is not just a regulatory requirement for businesses in the Home & Garden and Pest Control sectors; it is an essential component of a comprehensive health and safety strategy. By ensuring that your local exhaust ventilation systems are effective and compliant, you protect your employees' health, enhance your operational efficiency, and bolster your business's reputation.
As you navigate the complexities of maintaining a safe work environment, remember that investing in LEV testing and compliance not only preserves the well-being of your employees but can also lead to increased productivity and customer trust. Don't wait for issues to arise; make LEV testing a fundamental part of your business operations today.