The Revolution of Injection Molding of Plastics in Modern Business
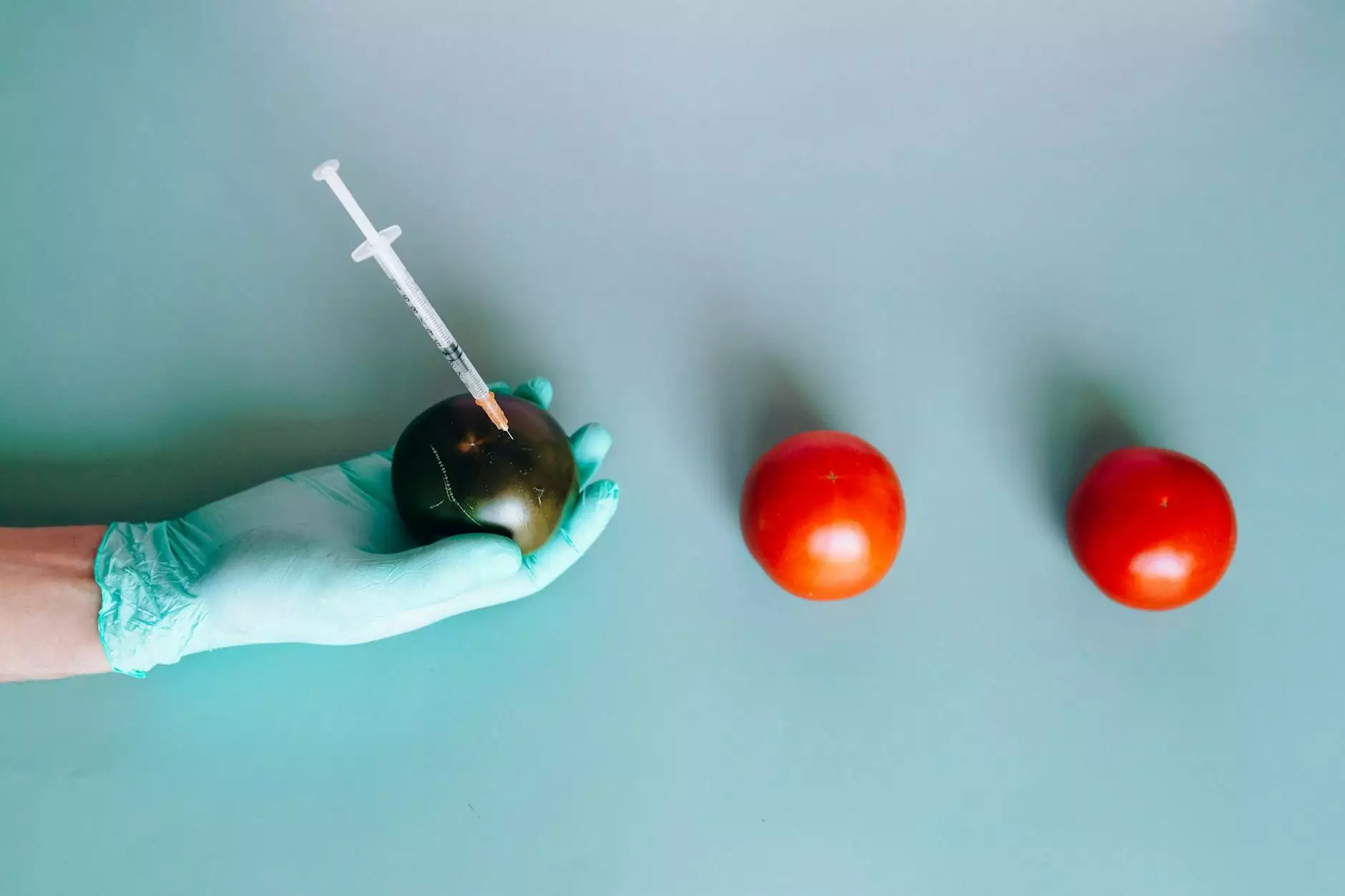
Introduction to Injection Molding of Plastics
The injection molding of plastics is a cutting-edge manufacturing process that has become indispensable in various industries. This method involves introducing molten plastic into a mold to create complex shapes with remarkable precision. As businesses strive for efficiency and cost-effectiveness, understanding this technology becomes vital.
The Process of Injection Molding
The injection molding process consists of several key stages:
- Material Preparation: Plastic pellets are fed into a hopper and heated until they melt.
- Injection: The molten plastic is injected into a pre-designed mold at high pressure.
- Cooling: The material cools and solidifies in the mold, taking its desired shape.
- Demolding: The solid plastic part is removed from the mold.
- Finishing: Any necessary post-processing, such as trimming or painting, is done to enhance the product.
Benefits of Injection Molding of Plastics
Businesses across various sectors have recognized the numerous benefits of utilizing the injection molding of plastics:
- Precision and Consistency: Injection molding allows for high precision, ensuring that each product is consistent in quality and dimensional accuracy.
- Efficiency: Once the mold is created, the production process is rapid, allowing for high-volume manufacturing.
- Material Versatility: A wide range of plastic materials can be used, including thermoplastics and thermosetting plastics, which easily adapt to various applications.
- Cost-Effectiveness: Although the initial costs of tooling can be high, the long-term savings from reduced waste and faster production make it economically viable.
- Complex Designs: Injection molding can produce intricate shapes that would be difficult or impossible with other manufacturing techniques.
Applications of Injection Molding
The injection molding of plastics finds applications in numerous fields, including:
1. Automotive Industry
Automotive manufacturers use injection molding to produce various components such as dashboards, bumpers, and interior parts. The ability to create lightweight yet strong components is essential for fuel-efficient vehicles.
2. Consumer Products
The consumer goods sector benefits greatly from injection molding, with products ranging from household items to toys. Mass production capabilities ensure that businesses can meet market demand efficiently.
3. Medical Devices
Injection molding is crucial for producing sterile and precise medical parts such as syringes, surgical tools, and containers. Quality control in this sector is paramount to ensure safety and compliance with regulations.
4. Electronics
The electronics industry utilizes injection molding for creating casings, connectors, and other intricate parts. With the continuous evolution of technology, the demand for complex designs has surged.
Challenges in Injection Molding
Despite its advantages, the injection molding of plastics is not without challenges:
- High Initial Tooling Costs: The creation of molds can involve significant upfront investments, which may be a barrier for small businesses.
- Material Limitations: Not all plastics can withstand the high pressures and temperatures involved in the process, limiting options.
- Potential for Defects: Common issues such as warping, sink marks, or short shots can affect product quality if not monitored closely.
The Future of Injection Molding in Business
The injection molding of plastics is continuously evolving with advancements in technology. The future may hold even greater efficiency through the use of:
1. Automation and Robotics
Automation in the molding process can lead to improved speed and consistency, reducing the likelihood of human error.
2. Sustainable Materials
The push for sustainability has prompted research into bio-based and recycled plastics, with injection molding adapting to these new materials.
3. 3D Printing Techniques
The integration of 3D printing into injection molding can allow for rapid prototyping and reduced time-to-market for new products.
Conclusion
As businesses in the metal fabricators sector and beyond continue to seek innovative and efficient manufacturing solutions, the importance of the injection molding of plastics cannot be overstated. Its ability to deliver precision, efficiency, and versatility makes it a critical element in modern manufacturing. By embracing this advanced technology, companies can ensure they remain competitive in a dynamic marketplace.
Call to Action
If you are looking to explore how the injection molding of plastics can benefit your business, contact us at DeepMould today. Leverage our expertise in metal fabrication and plastic injection molding to elevate your production capabilities.
© 2023 DeepMould. All rights reserved.